Bespoke Solutions in Aluminium
October 2016
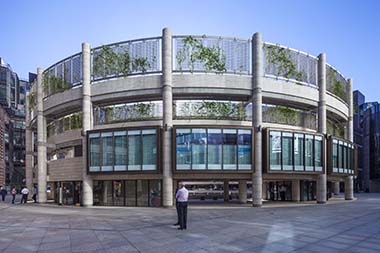 |
In an occasional feature for Aluminium in Architecture Wojciech Brozyna - MD of Aluprof UK reinforces the argument for specifying aluminium.
Why specify aluminium? Some of the reasons that spring to mind are ‘strength’, ‘durability’ and ‘recyclability’, it is the latter that makes the specification of aluminium a green choice for architects as aluminium is virtually 100% recyclable many times over. Today over 50% of all aluminium extruded comes from recycled content which uses just 5% of the original energy used to create the aluminium in the first place. So why don’t we just use more recycled aluminium, well, we just can’t get enough to meet demand! Since 1880, when aluminium became a commercial reality, 75% of all the aluminium produced is still in active service, I don’t think many other building materials can boast such credentials.
Compared to other materials used in fenestration, aluminium profiles are cheaper and quicker to produce, they are also capable of providing intricate shapes for various requirements. These designs help the profiles to achieve not only incredible strengths without reverting to other materials, they can also offer high levels of weathering performance.
When half-scales (the inside and outside aluminium profiles) are coupled with modern multi chamber polyamides and strategically located aerogel insulation profiles, insulation levels of the frame can meet the Passivhaus standard. Thermal insulation performance for openable windows can achieve a UW from 0.53 W/m2K and for a door, a UD from 0,62 W/m2K. So aluminium systems are definitely not behind other materials when it comes to insulation.
Recent studies in the industry suggest that coated or anodised aluminium systems can last the lifetime of a building, there are examples, such as the New Bodleian Library, now refurbished and known as the Weston Library. Here the original anodised aluminium windows on this building were installed in the 1930’s and when the facade was refurbished, were simply cleaned in-situ within the original facade. These windows have already provided an eighty-year productive life with at least the same life expectancy in the future.
These attributes have helped aluminium become the specified material of choice for architects when it comes to fenestration systems but, it is the ‘bespoke’ nature of today’s facades that really inspires the use of aluminium in architecture.
One of the most impressive food experiences in London can be found at Broadgate Circle near to Liverpool Street Station. The venue offers a diverse collection of restaurants, cafes, bars, street food traders and a gym. The construction makes extensive use of natural limestone with aluminium windows and doors supplied by Aluprof and expertly installed by Linder Facades. The result is a high quality development fit for the city.
Completed in early 2015, all aluminium profiles and pressings have been naturally anodised in C34 Bronze, which complements the natural limestone whilst offering a sustainable and very resilient finish.
Aluprof systems specified on the project included a bespoke version of the MB-SR50 curtain wall system with its distinctive rounded structural profile design, complete with a commercial entrance door system. The MB-86 which utilises a hidden leaf assembly which offers contemporary clean lines when used in the MB-SR50N curtain wall system but still utilises heavy duty hardware with high security locking options.
The bespoke element of the MB-SR50N curtain wall system is a specially designed external capping which offers a raised square feature and recess. The result offers a distinctive visual appearance of the framing system whist the main design of the system remains unchanged. It is here that the main issue of bespoke solutions work so well. Aluminium can easily be extruded in special shapes within a few weeks of final designs being approved, if the profiles are cosmetic or consist of typical details, there is no need to retest the system as the ‘performance’ of the system is not affected.
Concept drawings for new extrusions can be completed between systems company and architect, then once agreed, die drawings can be produced, from this stage it can be matter of six to eight weeks for the extrusion die to be made and extrusion to be readily available. These lead times are well within a new-build or refurbishment programme and open up possibilities for bespoke shapes of mullions, transoms and curtain wall cappings. The other areas of bespoke design, could be edge detailing to an existing or a new facade material, detailing to accommodate a special glazing detail, or special profiles which will allow CNC work to provide a unique visual appearance.
The only limit to bespoke design is the specifiers imagination.
Aluprof systems are increasingly being specified on a wide range of residential and commercial projects across the UK. Systems are designed, fabricated and installed by selected, specially trained companies to ensure each fabricated product meets the Aluprof exacting standards. Further information is available on the company website at www.aluprof.eu and specialist advice is available directly from Aluprof UK offices on 0161 941 4005. Fabricator and Installer of the bespoke facade, HKL Specialists can be contacted on 01623 550357.
|